- Services
- Industries
- Automotive
- Battery
- Building inspection
- Fire alarms system testing
- Household appliances
- Installation materials
- Industrial machinery
- IT & audio video
- Laboratory, test & measurement
- Lighting equipment
- Maritime, oil & gas
- Medical & healthcare equipment
- Military & aerospace product testing
- Wireless & telecom
- Resources
- About
- Blog
- Events
HALT/HASS testing
Highly Accelerated Life Tests (HALT) and Highly Accelerated Stress Screens (HASS) are designed to be a faster and more efficient way of fault finding than traditional testing methods. With HALT/HASS you can speed up the design and testing phase of your product in development and reduce failures in the field or to consumer. With robust and reliable product design, the results are savings in both time and cost.
HALT/HASS testing is designed to expose the possible failure modes and design flaws in a product. These weaknesses can be revealed in a matter of days instead of the weeks compared to traditional reliability or qualification testing. This results in accelerated development while reducing cost and can also prevent release of substandard product, reduce warranty costs incurred by the manufacturer and prevent or reduce costly downtime in operations.
HALT/HASS technology was introduced in the 1990s as a simple thermal shock chamber with a vibration table. Today, the technology is an integrated testing system that provides the extreme stresses necessary to rapidly find design flaws missed by traditional methods.
How is the test conducted?
The testing chamber combines extreme temperature cycling and repetitive-shock and vibration for accelerated stress testing. Random vibrations up to 75gRMS in force (10-5,000 Hz) in 6 degrees of freedom (DOF) are applied during rapid temperature changes, from -100°C to 200°C. The thermal chamber's conditioning system has vacuum-jacketed liquid nitrogen cooling and nichrome wire heating, with ramp rates of 60-100˚C per minute.
What type of errors or failures can these tests reveal?
HALT/HASS
1. Design failures
- Insufficient frequency margins
- Mounting points
- Material choice
2. Production errors
- Early life failure due to contamination
- Solder faults
- Latent faults
3. Components failures
- Board layout design
- Weight of board components
HALT vs HASS – what is the difference?
The terms HALT (Highly Accelerated Life Tests) and HASS (Highly Accelerated Stress Screen) are both used for accelerating testing. There is differentiation in the terms based on the stage of development of the product. HALT testing is done earlier in development on bare components and sub-assemblies of a product, which is a functional sub-assembly. There is an emphasis on rapid temperature changes as accelerate stress. Completed products ready for manufacturing, on the other hand, are subject to HASS testing, with greater focus on mechanical testing and more stable extreme temperatures, as the components within a product are less subject to rapid temperature changes.
Is this type of test relevant for your product?
Many industries benefit from HALT/HASS testing to ensure the durability of critical products. For example, products being used in aerospace, in the maritime or offshore industries or components used in combustion engines, must be capable of surviving harsh conditions, including vibration, extreme temperatures and rapid temperature changes. These methods of testing would also be beneficial for most R & D departments regardless of the industry they belong to; stress testing prototypes will allow organizations to understand the weak points of the products earlier so these can be fixed or be replaced by other solutions early in the design phase. That way costly delays or re-design in a later stage will not need to occur.
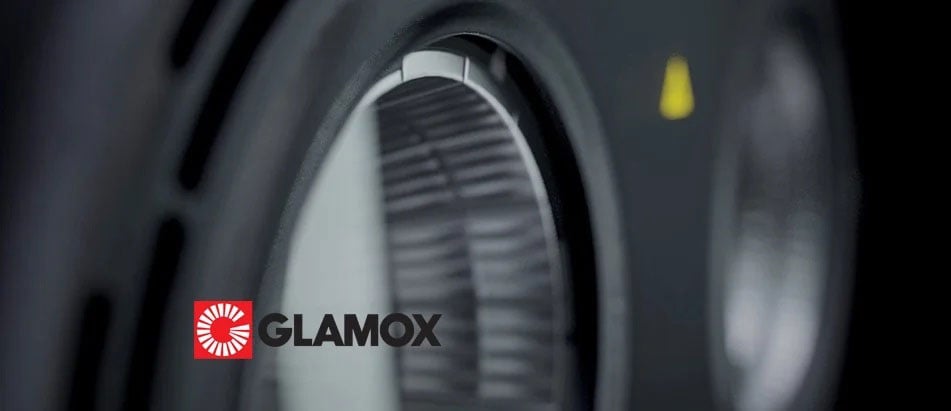
Glamox relies on Nemko for reliability and stress testing
Read more about how Glamox relies on Nemko for reliability and stress testing of their lighting products.
Profile: Omar Runcie and the role of HALT/HASS testing in product quality
With nearly 20 years of experience in the evaluation and testing of advanced technologies in a variety of industries, Omar has a first-hand understanding of the potential problems in new product designs, and how HALT/HASS testing can help mitigate them.
In a recent interview, Omar discussed the specifics of HALT/HASS testing and its importance in the development cycle of advanced electrical and electronic products.
See how it works